Product Returns Management
Simplified Returns That Keep
Customers Coming Back
- Fast and accurate processing: Every returned product is inspected, sorted, and restocked efficiently to minimize disruptions to your inventory management.
- Flexible return policy support: We help retailers enforce clear return policies that balance customer expectations with cost control, which reduces unnecessary losses.
- Data-Driven Returns Insights: We help you identify patterns and improve product quality while preventing future returns by tracking returns data and analyzing return rates.
Get a Free Quote
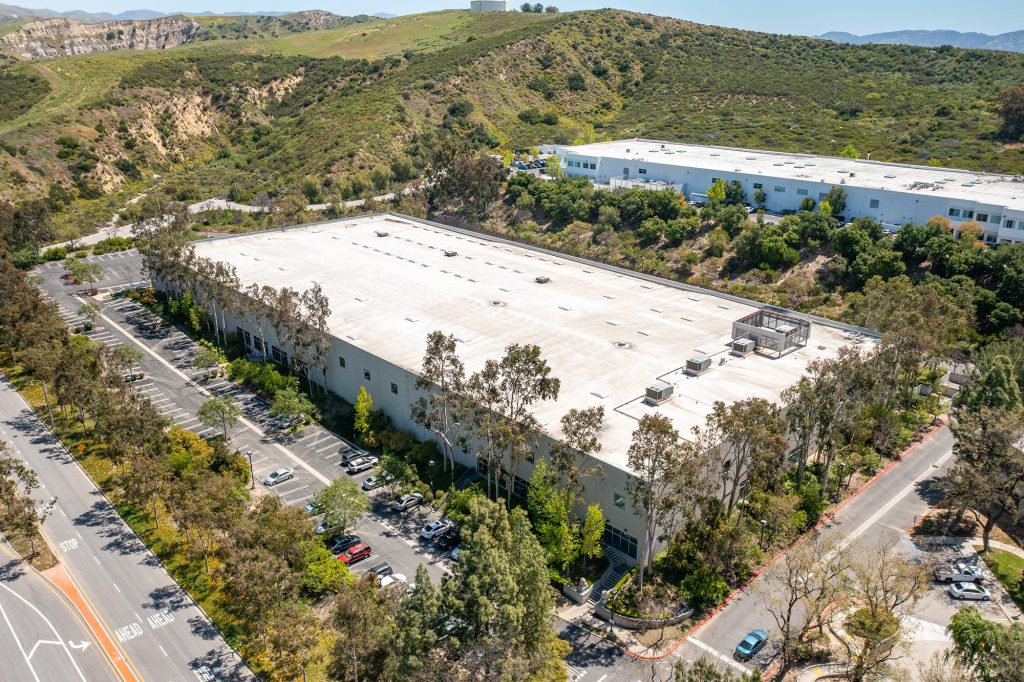
About Our Product Returns Management Service
Managing product returns can be complex, but it doesn’t have to be a burden on your business. Our returns management system is designed to simplify the entire returns process, from handling return requests to efficiently processing returns and restocking inventory. We provide effective returns management that improves customer satisfaction while protecting your bottom line regardless of whether you’re a retailer dealing with high-volume ecommerce returns or looking for a better way to manage customer returns.
We ensure that every returned item is inspected, categorized, and either restocked or processed for refund based on your returns policy. Our system tracks return rates, identifies controllable returns, and provides insights to help reduce unnecessary returns in the future. We also help businesses implement free returns strategies that balance customer retention with cost efficiency.
With our returns management software, you gain efficient returns processing, streamlined return shipping, and a structured returns management best practice approach to ensure a smooth return process for you and your customers.
River Plate Helped Me Feel Supported Every Step of the Way
“River Plate, Inc. is an amazing company with excellent communication and customer service. We’ve been with them for a few years now, and we are very thankful for the service we receive. Yolanda, Leo, and the rest of the team go above and beyond for their clients, and I really appreciate that.” – Frances Fregoso
Our Product Returns Management Process
Our structured returns management solution ensures that every return is handled quickly and accurately, which reduces costs and improves the return rate. From managing returns to optimizing the return management workflow, we make the process hassle-free for both businesses and customers.
Step 1 – Return Request and Authorization
|
Step 2 – Product Receipt and InspectionOnce the returned goods arrive at our facility, they go through a thorough inspection. This step ensures that each returned item matches the reason stated by the customer, which prevents abuse and identifies potential quality issues. |
Step 3 – Condition Assessment and Sorting
|
Step 4 – Restocking or Disposal HandlingEligible products are returned to inventory for resale, while unsellable goods are processed according to the retailer’s preferences—recycling, liquidation, or proper disposal. This improves inventory efficiency and minimizes losses. |
Step 5 – Refund, Replacement, or Exchange ProcessingCustomers expect happy returns, and we ensure a smooth resolution by quickly processing refunds, sending replacements, or facilitating exchanges. This step strengthens customer retention and improves brand trust. |
Step 6 – Returns Data Analysis and Process Optimization![]() Every return provides valuable insights. We analyze return rates, identify trends, and offer recommendations to reduce unnecessary e commerce returns. Businesses can minimize costs and enhance efficiency by continuously improving the returns management solution. |
Why Trust Us With Your Product Returns Management
Here is why you should trust us with your product returns management.
– Decades of Experience in Returns and Reverse Logistics
Handling product returns isn’t just about receiving returned goods. It’s also about keeping operations smooth and customer expectations met. With decades of experience, we’ve refined our returns management solution to balance efficiency and cost control. Whether you’re dealing with routine e commerce returns or complex reverse logistics, our expertise ensures minimal disruptions.
– Proven Accuracy in Refund and Replacement Processing
A poorly managed return process can frustrate customers and create unnecessary costs. We streamline refunds, replacements, and exchanges with strict accuracy controls. Every returned item is verified, processed, and handled promptly to maintain customer satisfaction and strengthen brand loyalty.
– Advanced Technology for Real-Time Inventory Updates
Keeping track of returned merchandise is just as important as selling new products. Our returns management system provides real-time updates on inventory, which ensures that resellable products are quickly restocked and flagged items are accounted for. Businesses stay informed, which also reduces stock imbalances and delays.
– Tailored Return Solutions for Every Business Model
No two businesses face the same returns process challenges. We create customized returns management best practices that align with your return policy regardless of whether you’re a retailer, an ecommerce brand, or a subscription-based company. Our flexible approach helps you maintain control while keeping customer returns simple and stress-free.
About Us
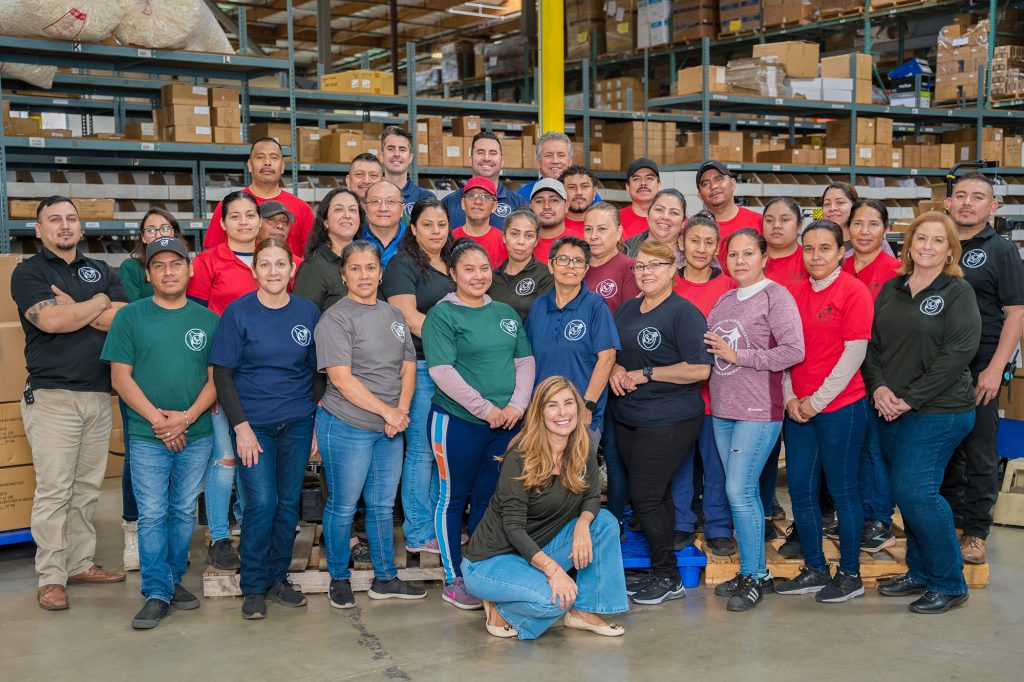
River Plate, Inc. started as a small, family-owned trucking company in Southern California in 1992. Back then, we focused solely on transportation, but as our customers’ needs evolved, so did we. They wanted storage, cross-docking, and fulfillment services, so we expanded.
Over the years, we grew into a full-service fulfillment center and started offering pick and pack, kitting, assembly, and inventory management. What began as a logistics company transformed into a trusted fulfillment partner, which supports businesses of all sizes with customized solutions.
Our success comes from hard work, strong relationships, and a commitment to service. Most of our early clients came from word-of-mouth referrals, and that tradition continues today. Whether you need ecommerce fulfillment, warehousing, or returns management, we handle it all with precision and care.
At River Plate, our primary job is to help businesses grow. Let’s talk about how we can support yours.
We Integrate With All Ecommerce Platforms
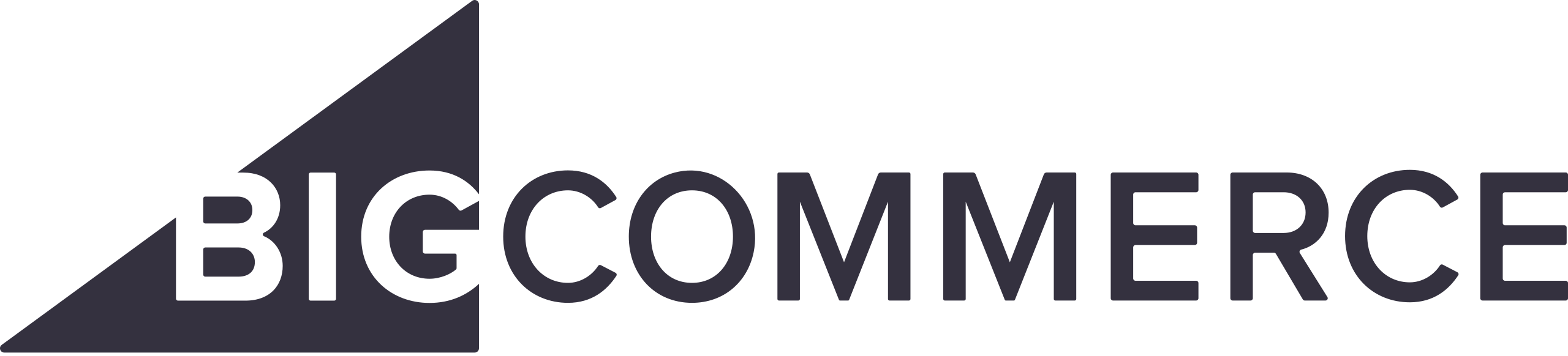
We connect seamlessly with BigCommerce and streamline your fulfillment processes for faster and more efficient order management.
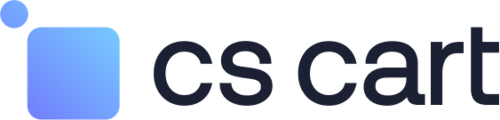
Our integration with CS-Cart ensures smooth handling of inventory and shipping for a hassle-free ecommerce experience.
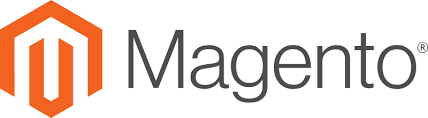
We integrate with Magento and Magento2 and simplify complex order management and enhance your fulfillment efficiency.

Our OpenCart integration helps you automate order processing and keep your customers satisfied with timely deliveries.
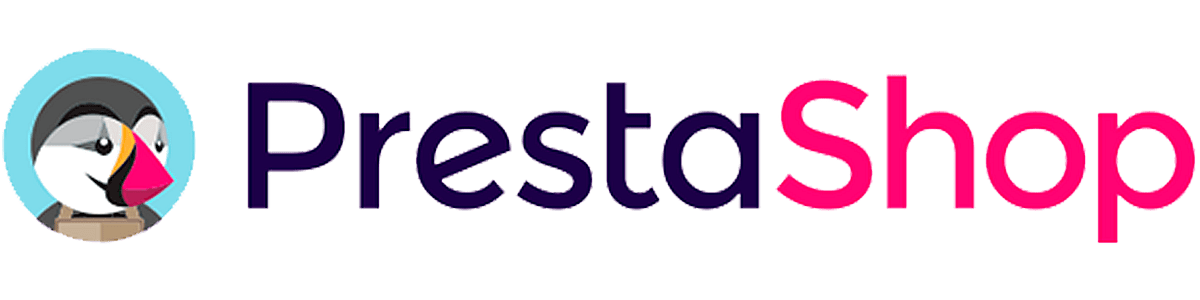
We work with PrestaShop to optimize your inventory management and improve shipping workflows.

Our Shopify integration delivers a seamless experience and syncs your store with our advanced fulfillment solutions.
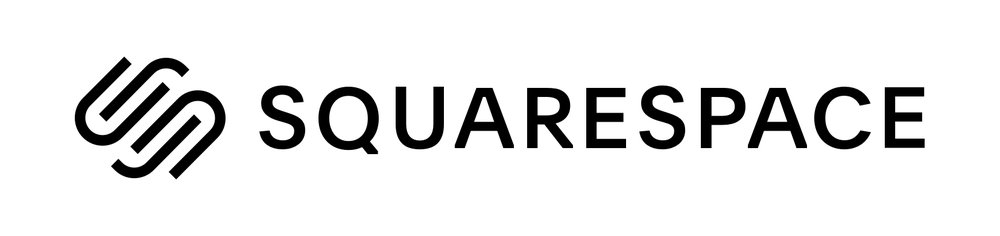
We streamline Squarespace fulfillment by automating inventory and shipping, which ensures timely delivery for your customers.

Our Volusion integration simplifies your logistics, from inventory tracking to shipping updates.
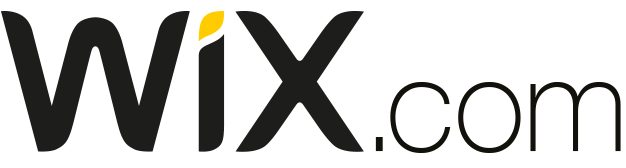
We connect with Wix to help you manage your ecommerce operations more efficiently, from orders to deliveries.
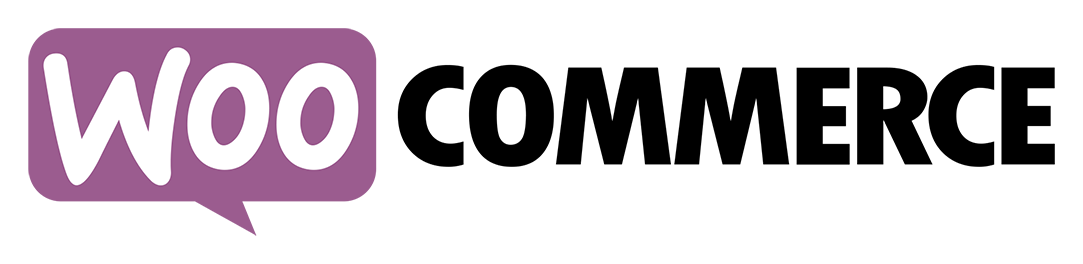
Our WooCommerce integration ensures accurate inventory management and on-time order fulfillment.
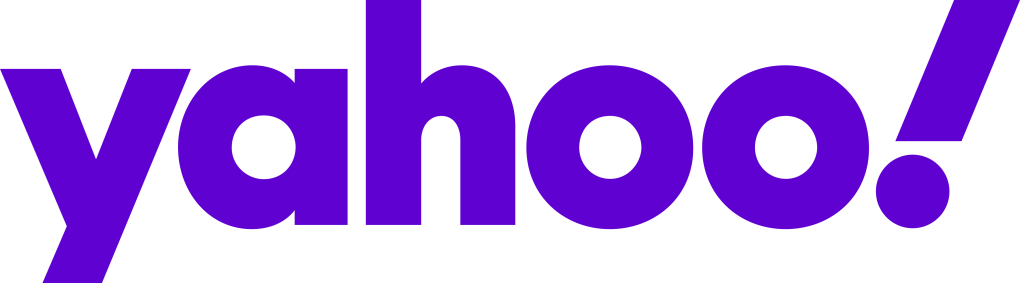
We integrate with Yahoo stores to streamline shipping and keep your operations running smoothly.
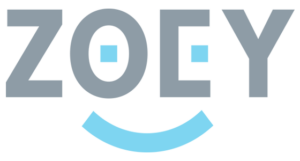
Our Zoey integration helps automate your order fulfillment and enhance customer satisfaction.
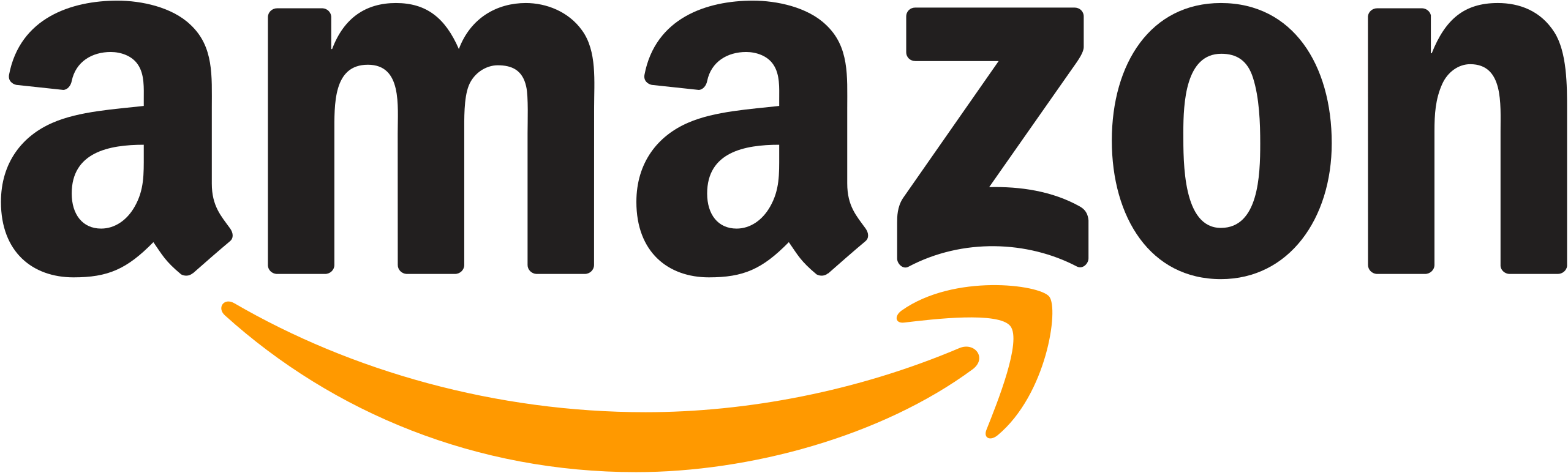
We integrate with Amazon to provide seamless order fulfillment and inventory management for your Amazon store.
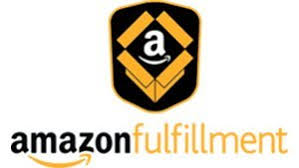
Our Amazon Direct Fulfillment integration ensures smooth processing and timely shipments directly to your customers.
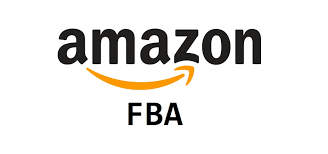
We handle Amazon FBA Restock seamlessly, which ensures your inventory stays optimized and ready for fulfillment.

Our ChannelAdvisor integration helps centralize your marketplace operations for streamlined inventory and order management.
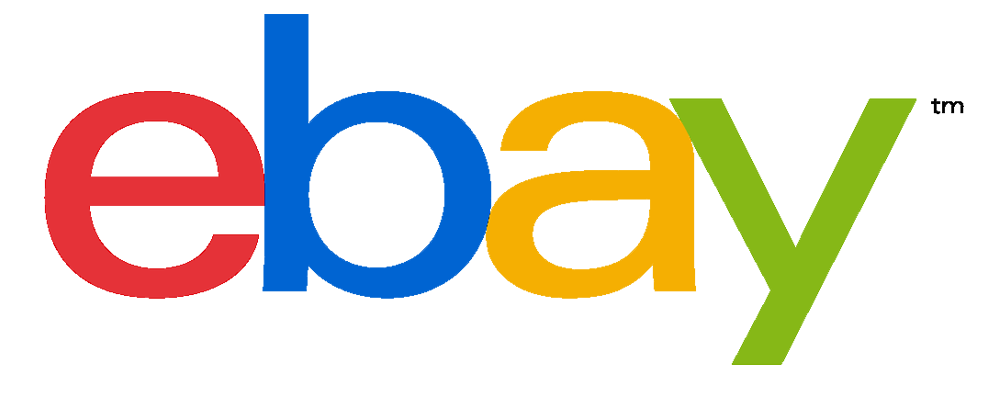
We connect with eBay to automate fulfillment, which helps you process and ship orders quickly.
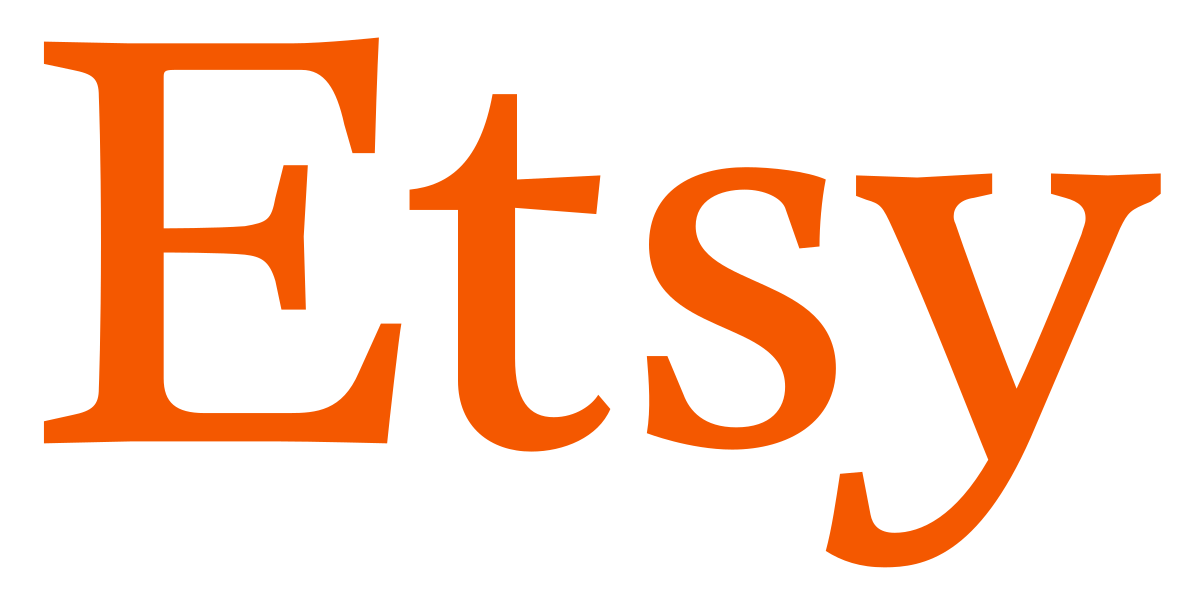
Our Etsy integration ensures accurate inventory tracking and efficient shipping for handmade and unique items.

We streamline fulfillment for Faire orders, which helps your wholesale customers receive their shipments on time.

We work with Goldbelly to manage fulfillment, which ensures your specialty food products arrive fresh and on schedule.

Our Groupon Goods integration simplifies bulk order processing and improves delivery efficiency.
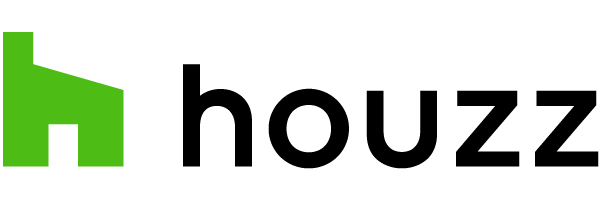
We support Houzz fulfillment by managing inventory and shipping for home and decor retailers.
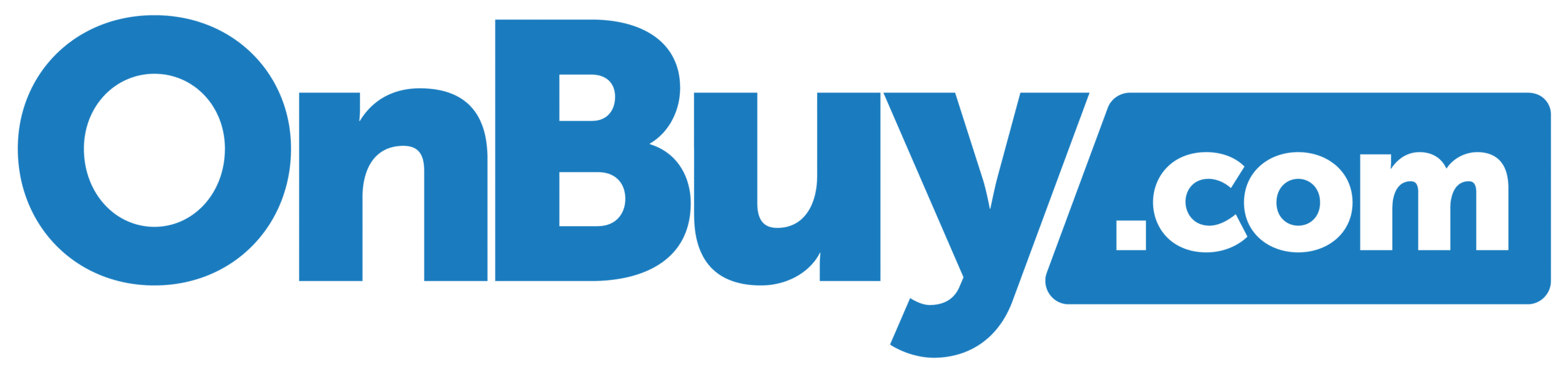
Our OnBuy integration ensures smooth order handling and reliable delivery for your marketplace sales.
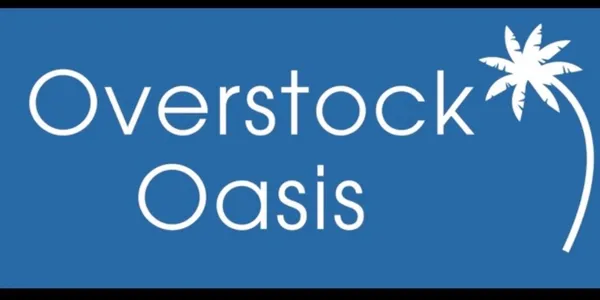
We optimize Overstock (Oasis) fulfillment, from inventory management to timely shipping.
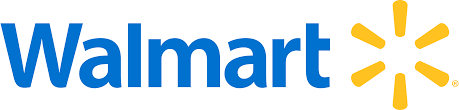
We integrate with Walmart to manage orders, reduce fulfillment times, and enhance customer satisfaction.
Our Wayfair integration ensures accurate inventory tracking and efficient delivery for home and furniture products.
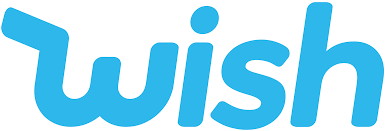
We streamline Wish fulfillment and help you manage orders and deliver products to customers quickly and efficiently.
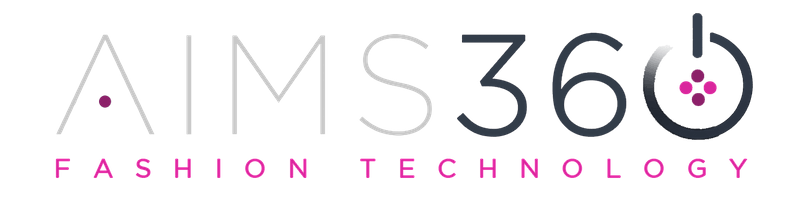
We integrate with AIMS360 to streamline order processing and inventory management for fashion and apparel businesses.
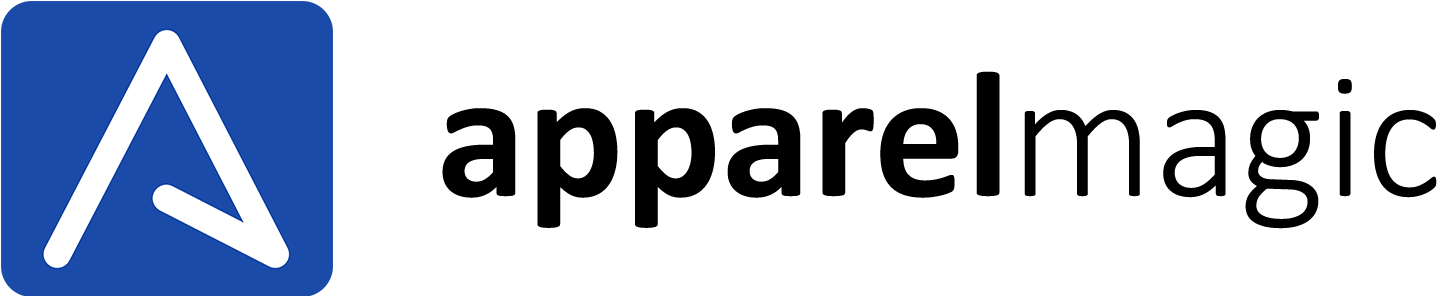
We connect with ApparelMagic to provide seamless inventory tracking and order fulfillment for the fashion industry.
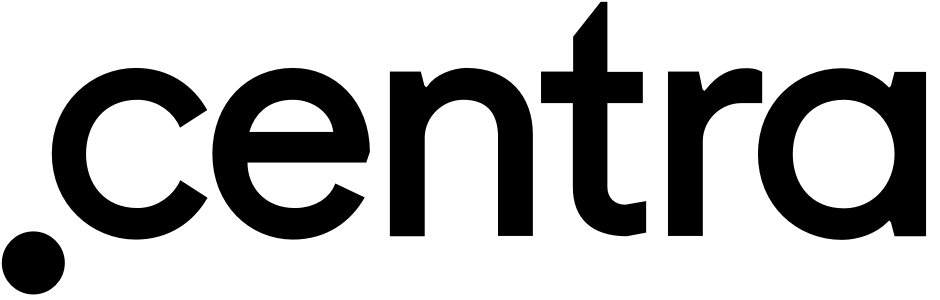
Our Centra integration helps centralize ecommerce operations, which ensures efficient order processing and inventory updates.
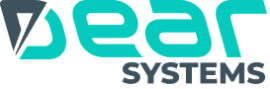
We integrate with Dear Systems to offer real-time inventory tracking and streamlined order management for your business.
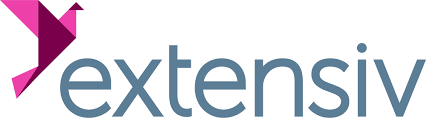
Our Extensiv 3PL Warehouse Manager integration optimizes warehouse operations and ensures fast and accurate order fulfillment.
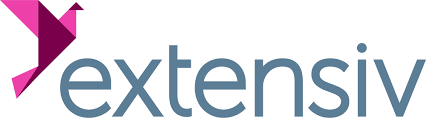
We work with Extensiv Order Manager to synchronize orders across channels, which improves efficiency and reduces errors.
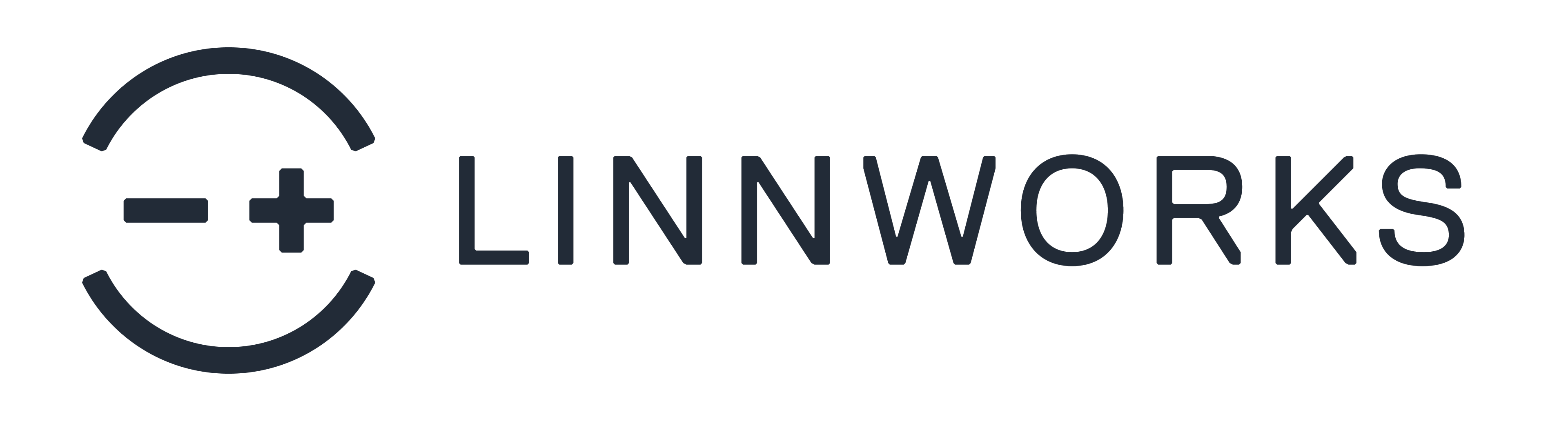
Our Linnworks integration automates order fulfillment and inventory updates across multiple marketplaces.

We integrate with NetSuite to offer a complete solution for managing orders, inventory, and fulfillment in one platform.
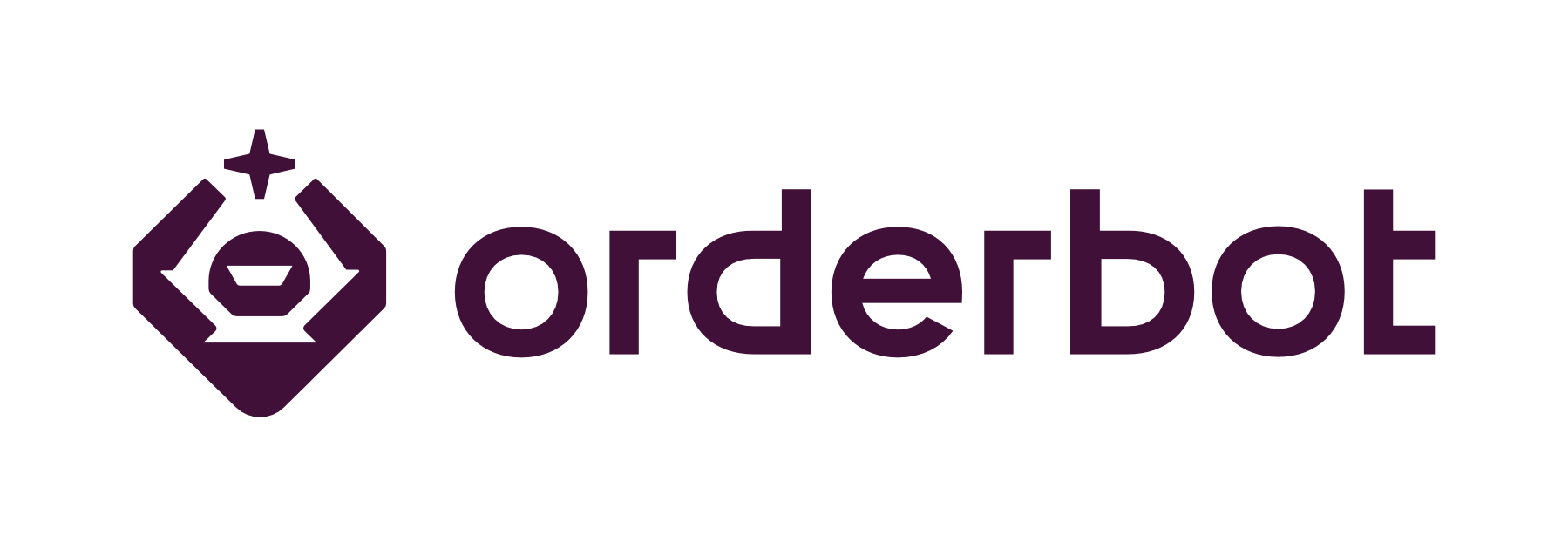
Our Orderbot integration simplifies order processing, which ensures accurate inventory tracking and timely deliveries.
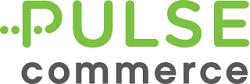
We work with PulseCommerce to automate order fulfillment, improve inventory accuracy, and enhance customer satisfaction.
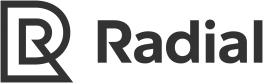
Our integration with Radial ensures seamless management of inventory, orders, and shipping for omnichannel businesses.
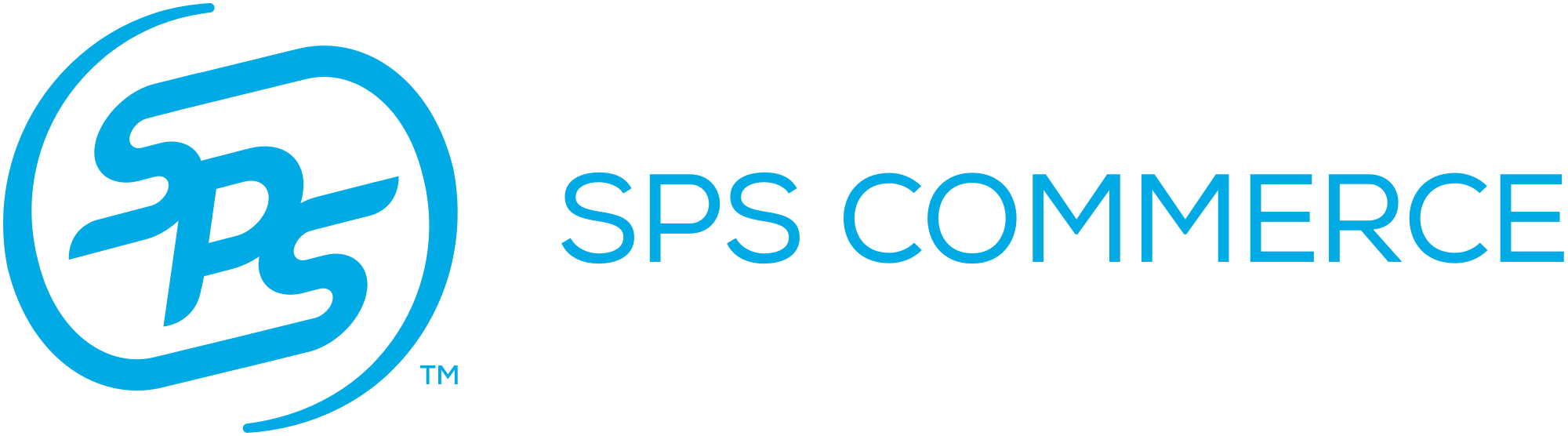
We connect with SPS Commerce to streamline electronic data interchange (EDI) for accurate order and inventory processing.
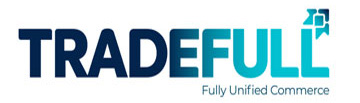
Our Tradefull integration centralizes your operations and simplifies fulfillment and inventory management across platforms.

We partner with TrueCommerce to provide seamless EDI and order management solutions, which ensures accuracy and efficiency.
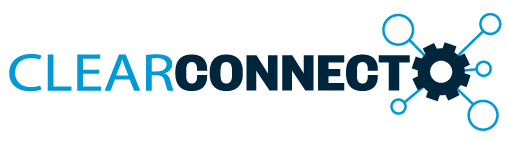
Our Uniware Clearconnect integration improves inventory synchronization and automates order fulfillment for smooth operations.
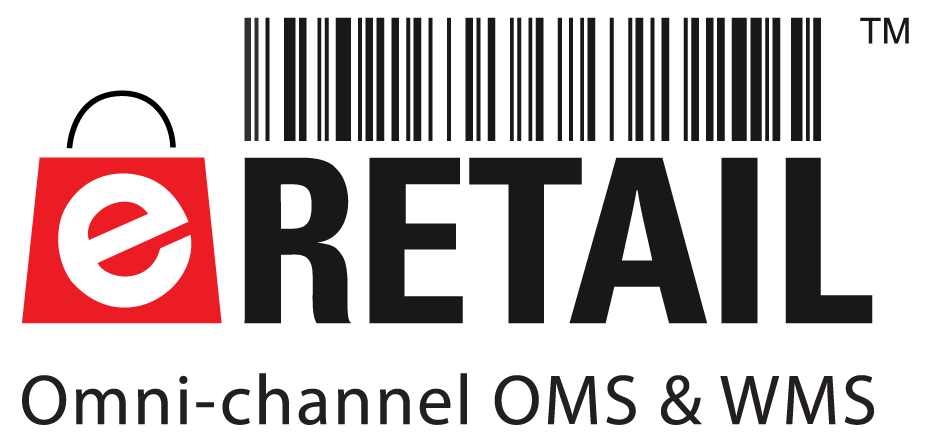
Our Vin eRetail integration helps you manage orders, inventory, and fulfillment seamlessly across multiple sales channels.
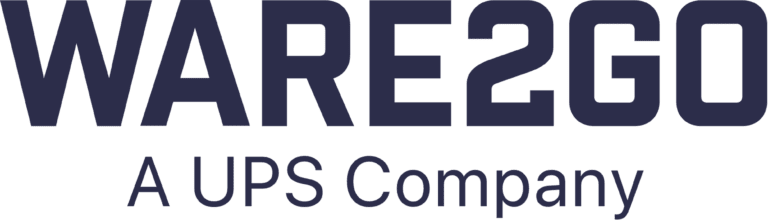
We partner with Ware2Go to provide scalable, fast, and reliable fulfillment solutions tailored to your business needs.
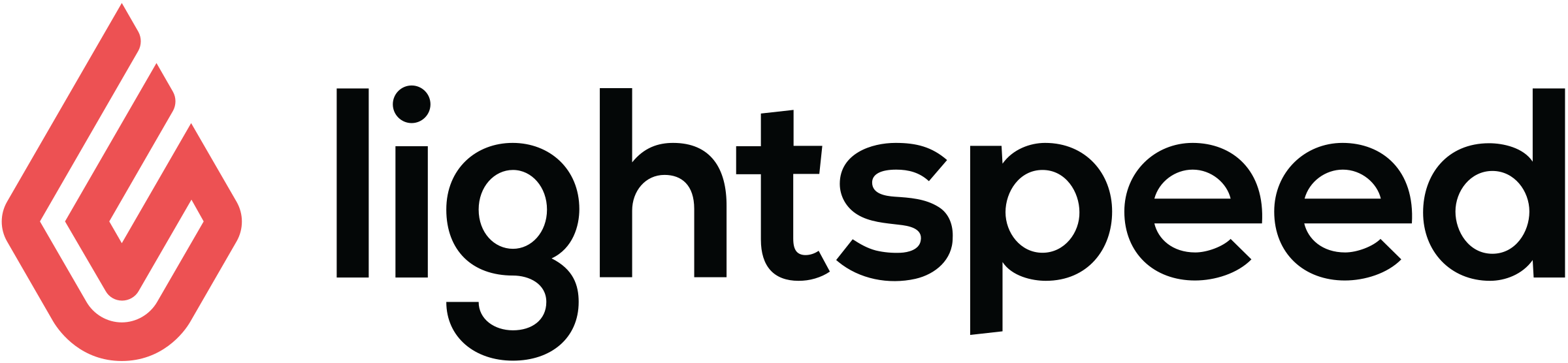
Our Lightspeed Retail integration connects your in-store and online sales, which ensures accurate inventory and efficient order processing.
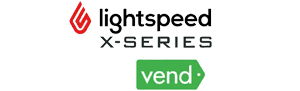
We streamline your Lightspeed X-Series (Vend) operations by syncing inventory and automating order fulfillment across channels.
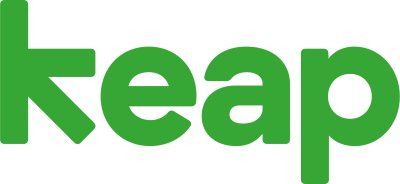
Our Keap integration helps you manage customer data and streamline order fulfillment, which creates a seamless customer experience.
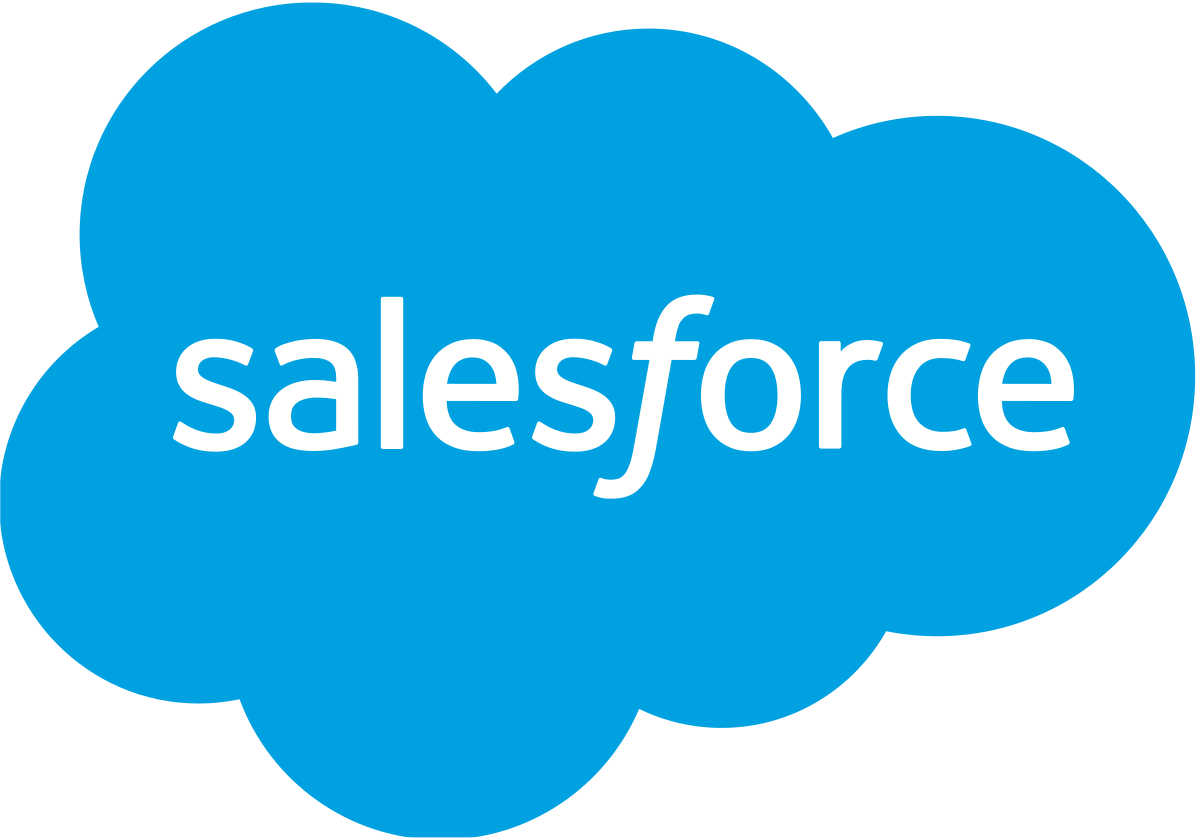
We integrate with Salesforce to synchronize customer data and improve fulfillment workflows for better business insights.
What Clients Have to Say About our Ecommerce Fulfillment Services
Professional and Helpful |
|
|
Friendly and Reliable |
|
|
Exceptional Customer Service |
|
|
What You Get When You Work With Our Product Returns Management Service
Here is what you get when you work with our product returns management service.
– Seamless Returns Processing for Faster Resolution
We streamline every step of the returns process, from authorization to resolution, which ensures quick turnarounds that keep customers happy and operations smooth.
– Thorough Inspection and Quality Control
Each returned item undergoes a detailed inspection to determine whether it can be restocked, refurbished, or disposed of, which reduces losses and maintains product integrity.
– Real-Time Tracking and Visibility
With real-time inventory updates, you’ll always know the status of returned goods, which can help you make informed decisions and prevent stock discrepancies.
– Flexible Restocking and Disposal Solutions
Not every returned product belongs back on the shelf. We offer customized restocking, liquidation, and disposal options to maximize recovery value and minimize waste.
– Cost-Effective Reverse Logistics
Our returns management solution optimizes shipping and handling costs and prevents unnecessary expenses while also ensuring a more efficient supply chain.
– Enhanced Customer Satisfaction and Retention
A hassle-free return experience builds trust and keeps customers coming back. With fast refunds, replacements, and exchanges, we help protect your brand reputation and improve customer retention.
Additional Services
Wholesale / B2B / Retail Fulfillment
We handle wholesale, B2B, and retail fulfillment with precision. Routing guides, palletized shipments, and compliance management are all part of our service. Every step is designed to keep your supply chain running smoothly.
Parcel Optimization
Shipping costs drop when you optimize effectively. We analyze your packaging, compare carrier options, and adjust rates. This tailored approach leads to cost-effective and efficient solutions.
Ecommerce Fulfillment Services
Fast, accurate fulfillment is key to success. From managing inventory to shipping orders, we’ve got you covered. Our advanced systems and strategic locations help you scale seamlessly.
Value Added Services
A great presentation leaves a lasting impression. With labeling, custom packaging, and quality checks, we make sure your products stand out. Every detail is handled to boost customer satisfaction.
Warehousing
Our secure warehouses provide flexible storage to fit your needs. Strategically located facilities ensure efficient organization and quick shipping. Real-time inventory tracking keeps you informed every step of the way.
Fulfilling orders across multiple platforms requires precision. We manage ecommerce, retail, and wholesale orders seamlessly. Accurate and timely processing ensures your customers are never left waiting.
Cross-Docking Services
Skip unnecessary storage and move goods faster. Cross-docking transfers shipments directly from arrival to delivery. This process reduces storage time and improves overall efficiency.
Kitting Services
We combine multiple items into one accurate, ready-to-ship package. Kitting services streamline your order process and improve delivery times. Every kit is prepared with care to meet your standards.
Amazon FBA Prep and FBM
We provide Amazon FBA and FBM preparation services, which include labeling, packaging, and compliance to meet Amazon’s strict requirements.
Freight Logistics
Domestic and international freight solutions ensure timely deliveries. We plan and execute shipments of all sizes with precision. Cost-effective transportation keeps your business moving forward.
Inventory Management
Our advanced Warehouse Management System (WMS) keeps your inventory organized. Real-time tracking provides full visibility and control over your stock at all times. Stay efficient and ready to meet demand.
Frequently Asked Questions
We support a wide range of industries, including ecommerce, fashion and apparel, electronics, health and beauty, home goods, and subscription box services. Our flexible returns management system adapts to different product types, which ensures a streamlined process for every business.
Yes, we manage international returns and cross-border logistics with a global network of carriers and warehouses. We ensure compliance with international shipping regulations, customs requirements, and localized return processing for a smooth customer experience.
Most returns are processed within 24 to 72 hours, depending on product inspection, return volume, and your specific policy requirements. Our efficient workflows ensure minimal delays, which keeps customers satisfied and inventory updated in real time.
We integrate with all major ecommerce platforms, order management systems, and third-party returns management solutions. Our API connections and automated workflows ensure seamless data synchronization for efficient return tracking.
Yes, we offer eco-friendly disposal, recycling, and refurbishment options to minimize waste and maximize product recovery. We work with certified recycling partners to ensure responsible handling of unsellable returns.
We optimize return shipping, implement bulk processing discounts, and provide strategic restocking solutions to lower costs. Our data-driven insights help identify trends to reduce unnecessary returns and improve overall efficiency.